The Transformative Power of **Plastics Injection Mold** in Modern Manufacturing
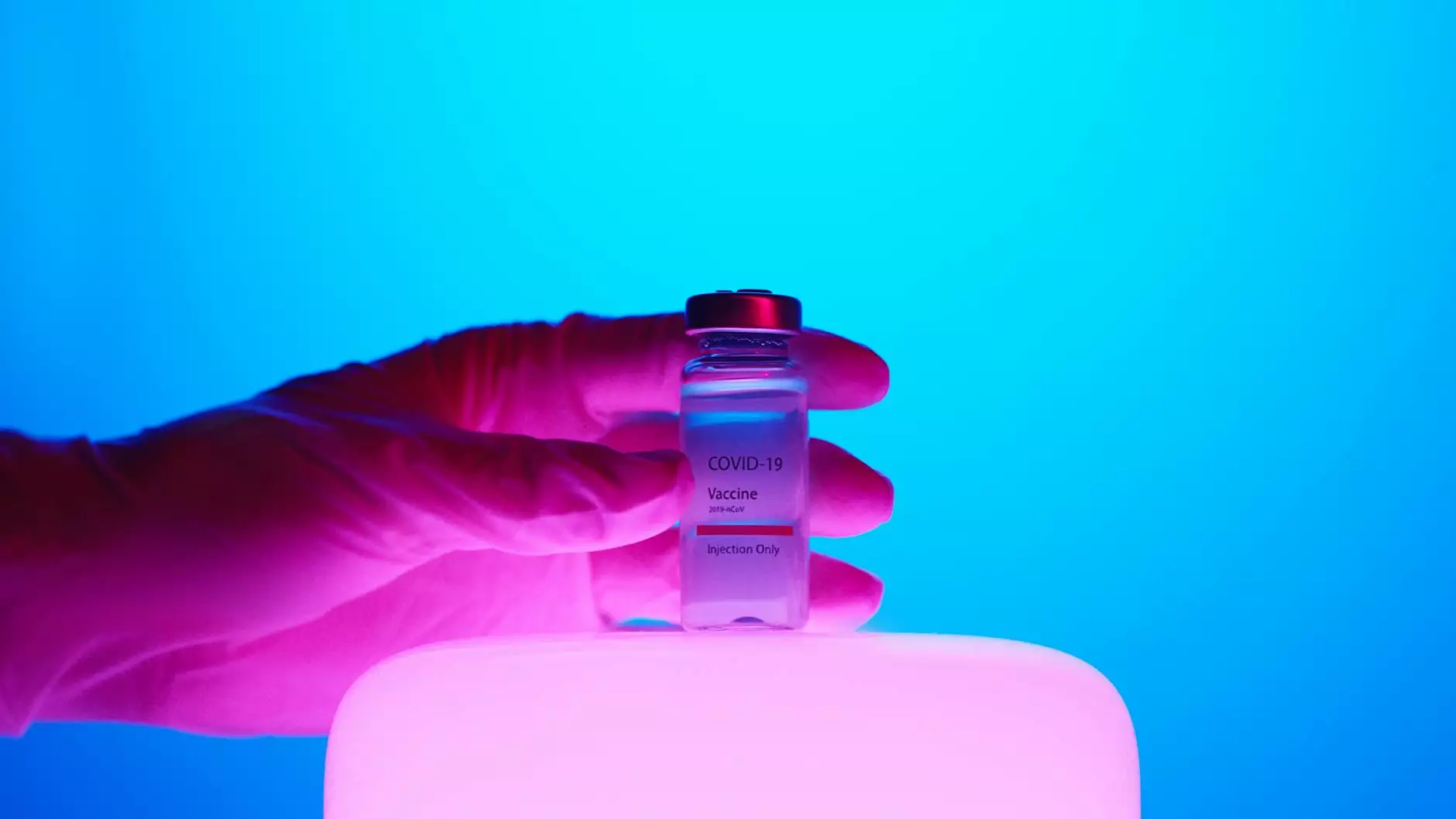
The plastics injection mold industry represents a critical sector in today's manufacturing landscape. As businesses seek out innovative solutions to enhance production efficiency and product quality, the significance of plastics injection molding continues to escalate. This article delves into the intricacies of this remarkable process, its benefits, applications, and its profound impact on metal fabricators and the broader manufacturing domain.
What is Plastics Injection Molding?
At its core, plastics injection molding is a manufacturing process that involves injecting molten plastic material into a mold to create a specific shape. This method is widely used for producing a variety of products, from small components to large assemblies. The process is known for its precision, speed, and ability to create complex shapes with high accuracy.
How Does the Plastics Injection Molding Process Work?
The plastics injection molding process can be broken down into several crucial steps:
- Designing the Mold: The first step involves designing a mold that meets the specifications of the desired product. This includes considering dimensions, geometry, and material properties.
- Melting the Plastic: Plastic pellets are fed into a hopper and then heated until they become molten. This is a critical step as the temperature and viscosity of the molten plastic must be carefully controlled.
- Injecting the Plastic: Once the plastic is molten, it is injected into the mold under high pressure. This ensures the material fills every cavity of the mold.
- Cooling: After injection, the mold is cooled to solidify the plastic. Cooling time is crucial as it affects the overall cycle time of production.
- Removing the Product: Once cooled, the mold is opened, and the finished product is ejected. This step may also include post-processing operations, such as trimming and finishing.
Benefits of Plastics Injection Molding
The advantages of plastics injection molding are numerous and diverse, making it a preferred manufacturing process for many industries:
1. High Efficiency and Speed
One of the primary benefits of plastics injection molding is its ability to produce parts quickly and efficiently. The process can cycle a complete product in a matter of seconds to minutes, significantly reducing lead times compared to other manufacturing methods.
2. Superior Precision and Quality
Injection molding allows for intricate designs and high tolerances, ensuring a consistent and accurate product. This precision is particularly beneficial for industries such as automotive and aerospace, where component quality is paramount.
3. Cost-Effectiveness in Large Quantities
While the initial investment for mold creation can be high, the per-unit cost decreases significantly with larger production runs. This makes plastics injection molding a cost-effective solution for high-volume manufacturing.
4. Versatile Material Options
A wide range of plastic materials can be used in the injection molding process, from thermoplastics to thermosetting polymers. This versatility allows manufacturers to select materials that best meet their product requirements.
5. Minimal Waste Production
Plastics injection molding is a resource-efficient process that minimizes waste by recycling excess material. Any unused or excess plastic can often be regrinded and reused, further enhancing sustainability.
Applications of Plastics Injection Molding
The applications of plastics injection molding are virtually limitless, impacting numerous industries:
1. Automotive Industry
In the automotive sector, plastics injection molded components are used for everything from dashboards to exterior panels. The lightweight nature of plastics contributes to improved fuel efficiency and safety.
2. Consumer Products
Household items, toys, and electronic gadgets often utilize plastics injection molding for their production. This process enables manufacturers to create products with innovative designs and durability.
3. Medical Devices
The medical field relies heavily on plastics injection molded components for devices such as syringes, IV bags, and various surgical instruments. The precision and cleanliness of the molding process are critical to ensuring patient safety.
4. Packaging
From food containers to cosmetic packaging, plastics injection molding is instrumental in creating safe, efficient, and attractive packaging solutions. The ability to produce lightweight yet durable containers is a significant advantage in this sector.
Why Metal Fabricators Should Consider Plastics Injection Molding
For metal fabricators, incorporating plastics injection molding into their manufacturing toolkit opens up new avenues for innovation and efficiency:
1. Complementing Metal Components
Plastics injection molding can be used to make supportive structures for metal parts, enhancing the overall assembly's strength and performance. This hybrid approach can lead to superior products.
2. Reducing Weight
In industries like aerospace and automotive, reducing weight without sacrificing strength is crucial. Metal fabricators can utilize plastics injection molded components to achieve this goal.
3. Expanding Product Offerings
By incorporating plastics injection molding into their operations, metal fabricators can diversify their product lines, tapping into new markets and customer bases. This strategic expansion can lead to increased revenue and business growth.
4. Enhancing Production Techniques
Plastics injection molding can improve production methods by streamlining assembly processes. When metal and plastic components work together seamlessly, manufacturers can reduce assembly time and costs.
Challenges and Considerations in Plastics Injection Molding
While plastics injection molding offers many benefits, it is not without challenges:
1. Initial Cost of Molds
The upfront costs for designing and creating molds can be significant. Businesses should carefully evaluate their production requirements to ensure that the investment pays off.
2. Design Complexity
Designing molds for intricate shapes requires expertise. Collaborating with experienced professionals is essential to avoid costly mistakes and ensure optimal mold performance.
3. Material Limitations
Though versatile, not all plastics are suitable for every application. Manufacturers must carefully select materials based on their physical and chemical properties to ensure product integrity.
The Future of Plastics Injection Molding
The future of plastics injection molding appears bright, with several trends shaping its evolution:
1. Technological Advancements
Emerging technologies such as 3D printing and automation are expected to enhance injection molding processes, leading to even greater efficiency and precision.
2. Sustainability Focus
With increasing attention on sustainability, the industry is moving toward more eco-friendly materials and processes. Biodegradable plastics and energy-efficient machinery are becoming more prominent.
3. Customization and Personalization
As consumer demand for personalized products grows, plastics injection molding will need to adapt to facilitate low-volume, high-variation production runs.
Conclusion
In conclusion, plastics injection molding stands as a cornerstone of modern manufacturing, significantly impacting various industries, including metal fabricators. Its efficiency, precision, and versatility position it as an essential process for businesses looking to innovate and excel in a competitive market. By understanding the ins and outs of this technology, companies can leverage its benefits to enhance their product offerings and drive growth.
For comprehensive insights and more information on how plastics injection mold can transform your manufacturing processes, visit deepmould.net.